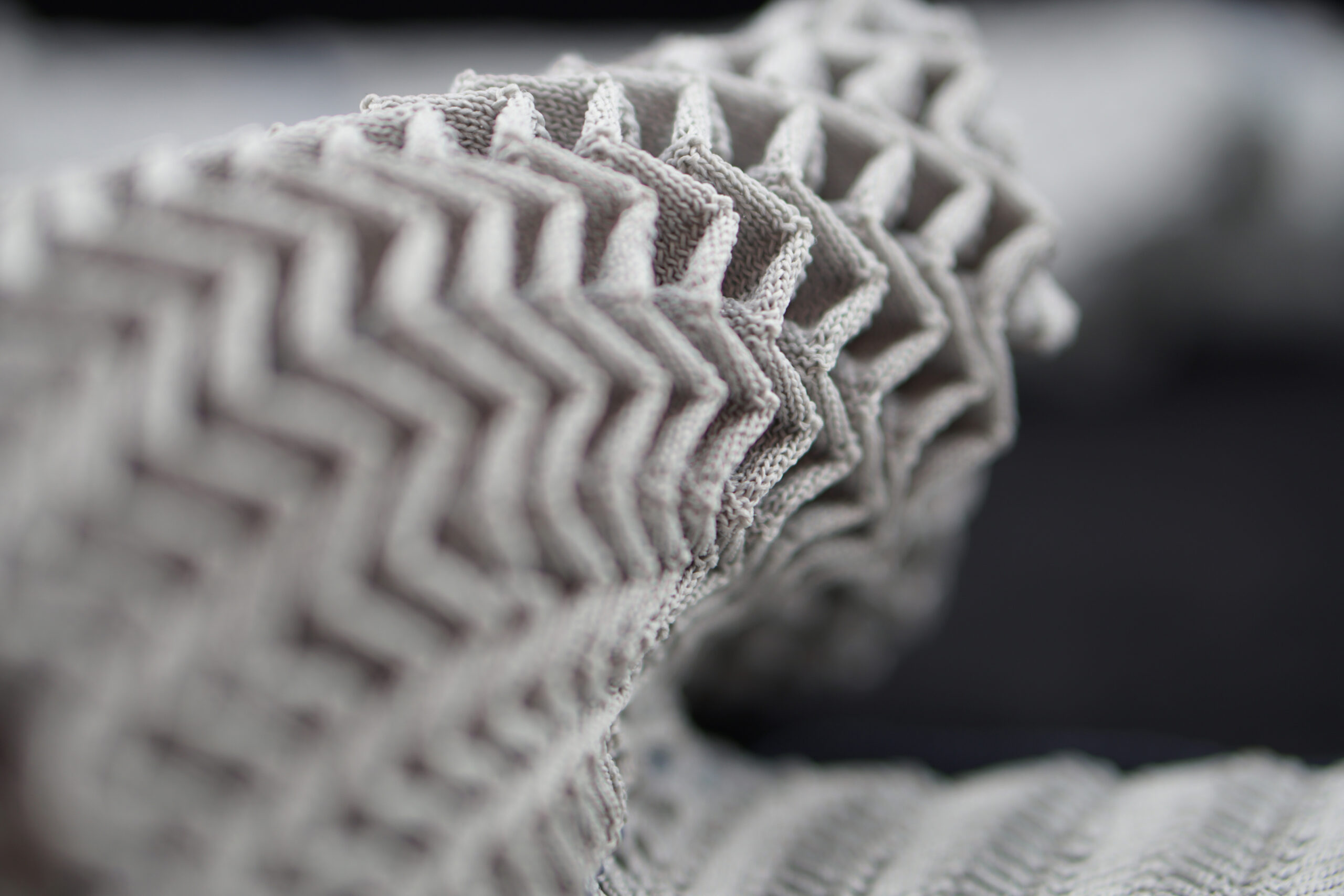
As thousands of Americans fired up their sewing machines to make masks last spring, Geneviève Dion, the director of Drexel’s Center for Functional Fabrics, was thinking about how her team could contribute to the nationwide effort to protect people from COVID-19. The group had barely settled into their new home — a state-of-the-art facility for prototyping and studying next-generation textile technology — when the pandemic hit, halting research and silencing the center’s array of digital knitting machines.
So, Dion did what she’s come to be known for at Drexel; she figured out a way to move forward.
“We adapted to help meet an urgent need,” she says. “We built the center to be able to go from prototyping to pilot production, and the pandemic made us prove we could do it.
Before her arrival at Drexel in 2007, Dion had already built a reputation for adapting the techniques and tools of fashion and industrial design to produce beautiful bespoke pieces.
In her work, Dion used the Shibori process, an ancient Japanese dying technique that involves binding and pleating fabric as it receives color, as a way to transform planar materials with unique three-dimensional patterns. To achieve her vision, she created her own tools to fold fabric and invented a process that permanently textures silk, earning her recognition as an innovator of the form. Her design work remains in the permanent collections of the de Young Museum in San Francisco and the Victoria and Albert Museum in London.
Creating new tools and processes sparked Dion’s curiosity about the emerging field of smart textiles and how fibers and fabrics can be imbued with new capabilities to produce textile devices. Coming from a labor-intensive couture world, she quickly recognized that developing advanced manufacturing processes for these new products would be essential.
“I was drawn to knitting,” Dion says, “because I recognized the need for automation and advanced manufacturing at the onset of the creation of smart textiles. Digital knitting can rapidly prototype a 3D form as a single piece and scale for manufacturing on the same equipment.”
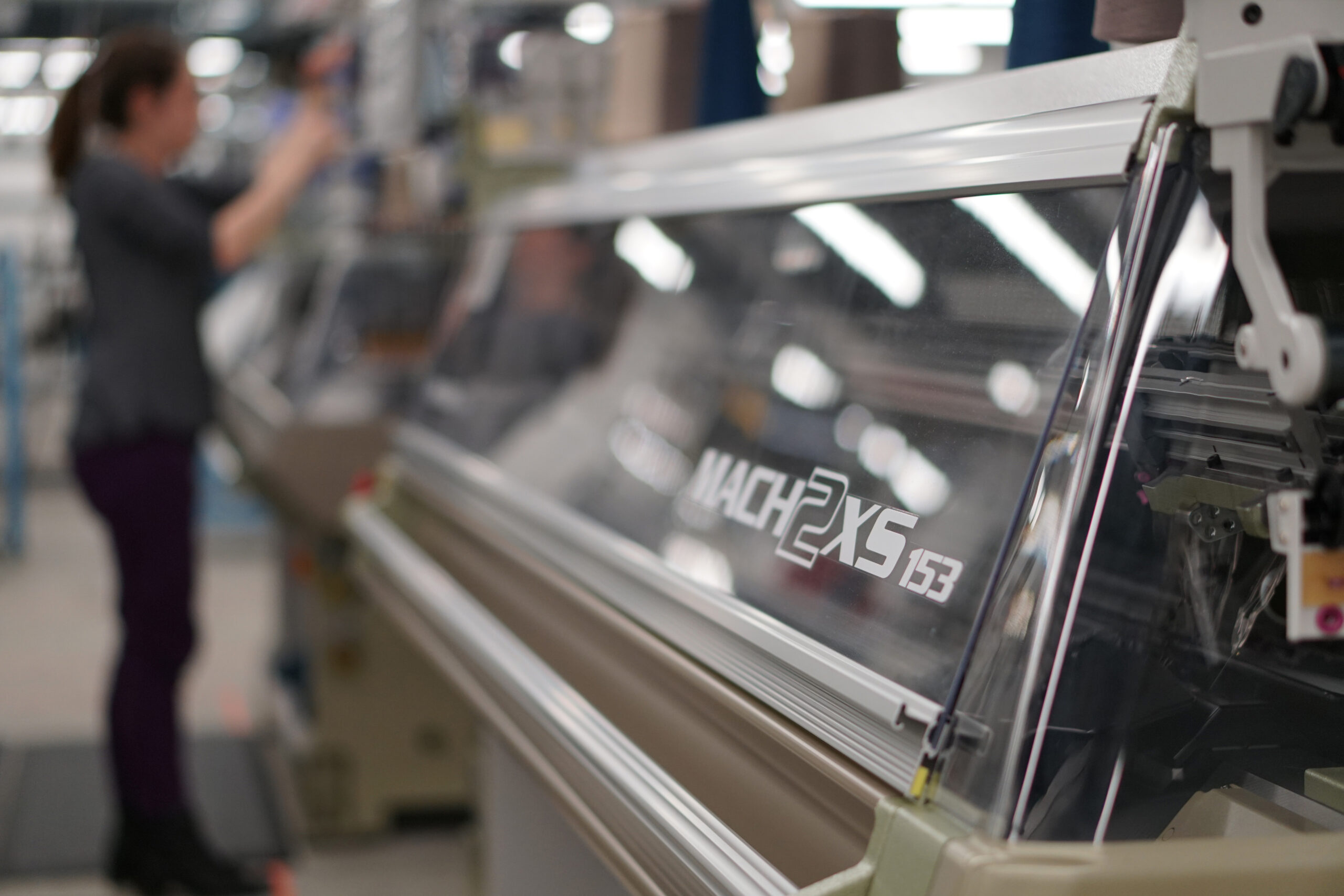
Dion’s curiosity led her to an associate professor role in Drexel’s Westphal College of Media Arts & Design, where she formed a partnership with Japan’s digital knitting machine manufacturer Shima Seiki to open one of the country’s first advanced textile research and innovation centers in 2012. With the University making strategic investments to expand its place in the city’s innovation economy, Dion’s center presented a unique opportunity to position Drexel as a leader in translational research around smart textiles.
Within four years, the single-machine operation had grown into Drexel’s 2,000-square-foot Center for Functional Fabrics and researchers from across the University were joining Dion to explore the challenges and possibilities of textile technology. The collaboration produced ventures into everything from conductive yarn and fabric antennas, to touch-responsive material and a computer program for designing and modeling the performance of advanced textiles.
Drexel’s focus on commercializing its research, coupled with its record of forming productive collaborations, caught the attention of the Department of Defense as it was building up a national initiative to spur innovation in manufacturing. As a member of the government’s Advanced Functional Fabrics of America (AFFOA), a $75-million public-private partnership consortium made up of government, industry and academics — which Drexel was invited to join in 2016 — Drexel set about transforming its Center for Functional Fabrics into a regional hub for studying, developing and commercializing textile technology.
Rising to the challenge once more, Dion and a team of partners from around the University, including President John Fry and Executive Vice Provost for Research & Innovation Aleister Saunders, added local and regional economic development funding to the University’s own investment and began renovating a 10,000-square-foot lab in the heart of both campus and Philadelphia’s Schuylkill Yards innovation neighborhood.
In the fall of 2019, Drexel opened its new Center for Functional Fabrics, a $7 million end-to-end research and development facility supported in part by the Commonwealth of Pennsylvania, and the home of the Pennsylvania Fabric Discovery Center (PA FDC).
“The center’s unique positioning at Schuylkill Yards highlights Drexel’s vision to be an intersection of innovation, where researchers, startups and companies gather to revitalize Philadelphia’s economy,” Saunders says. “It places the Center for Functional Fabrics right at the forefront of advanced manufacturing of functional fabrics.”
The center combines textile design and fabrication expertise with the ability to simulate a mass-production environment. It is built to explore new ideas, give them form and function and help others see the vision for their use. According to Stephen Luckowski, program manager for the Department of Defense’s Manufacturing Innovation Institutes, which includes AFFOA, these centers are intended to bridge what startup investors call “The Valley of Death” — the daunting and expensive prototyping, validating and problem-solving process that lies between promising concept and viable product.
A primary challenge in that process that the CFF team has been addressing stems from the fact that textile making — though one of civilization’s oldest forms of manufacturing — lacks the digital design tools to satisfy the technical requirements of functional fabric innovation.
“Up until 100 years ago, you only had four materials involved with textile making — its whole history was understanding these four fibers,” Dion says. “Now, there are many new materials enabling functional fabrics. And when you want to make a device with new functionality or performance, it requires precision and repeatable manufacturing, so you need to fully understand a textile’s behavior — right down to the fiber level.”
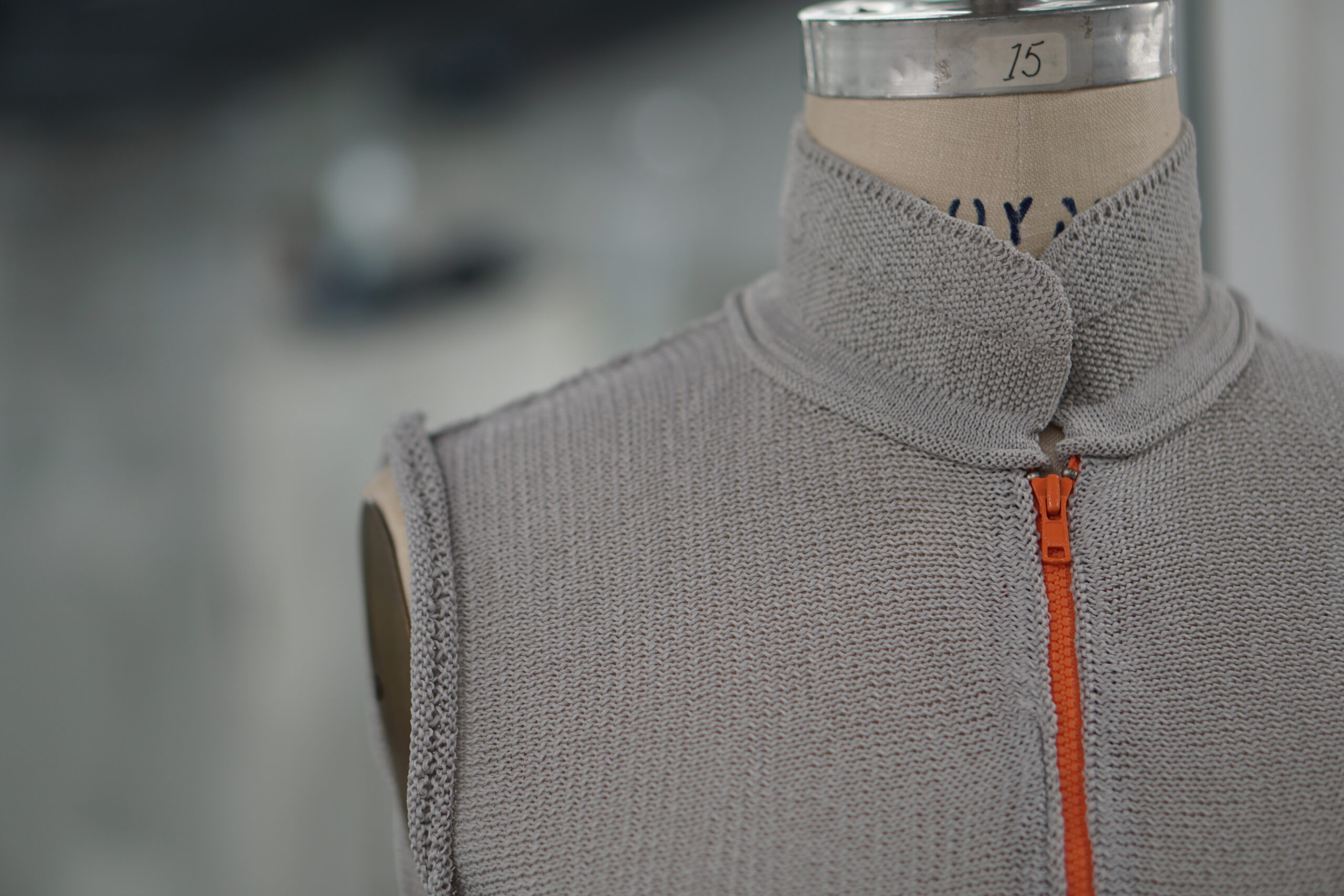
So, one of the center’s basic research pursuits is understanding and quantifying fibers and textiles in the same way engineers study the mechanical properties of structures like I-beams.
The center’s textile testing and characterization facility is helping the team uncover and compile this important information. In it, researchers, like textile engineer Chelsea Amanatides, can twist, bend, pull and rub textiles until they break — all the while microscopically observing their behavior. This data, combined with many years of information on samples, prototypes and yarn, is bolstering a database that Dion says will guide and enrich the center’s work.
The next task the team has undertaken is developing a design platform that can accurately model the behavior of textiles before they’re created — allowing manufacturers to minimize the need for trial and error when innovating new products.
In collaboration with David Breen, a professor of computer science in Drexel’s College of Computing & Informatics, the center is creating a data-driven fabric simulation tool. Breen’s background in cloth modeling and animation began in the 1990s with doctoral research, conducted with the Fashion Institute of Technology, that supported the fabric composite design efforts of helicopter-maker Sikorsky Aircraft. Now he’s using Amanatides’ foundational research to build a predictive modeling tool for knitted textiles, similar to those used by architects and engineers to envision and examine the behavior of solid structures.
The team, which also includes Randall Kamien, a physics professor with the University of Pennsylvania, has already made strides in identifying appropriate geometric structures to represent yarns within a textile, resulting in an initial patent application. This step will simplify the modeling computation and will enable rapid simulation of the internal complexity that dictates a textile’s behavior.
“Once you understand how the yarns work, you can build layers of abstraction upon that,” says Breen. “If we can model the yarns, we can then derive higher-order models based on that yarn structure.”
Addressing these fundamental challenges will eliminate a lot of the uncertainty from the innovation process and make it more accessible, and it could enable greater advances. Until the work is complete, however, researchers at the center are offering their experience in product design, prototyping and computer-aided manufacturing to support partners in industry, government and academia.
“As an industry person, partnering with Drexel is beneficial because I get to leverage their technology, and their knowledge of that technology,” says Eric Spackey, CEO of partner company Blue Water Defense and former chief marketing officer of AFFOA. “I may not have that same equipment, or I may not have the people who know how to run it. So, I can actually run concepts through them — to say ‘hey, would this work?’ Could you make this material so it’s thinner, lighter, stronger, than I can on my current equipment?’”
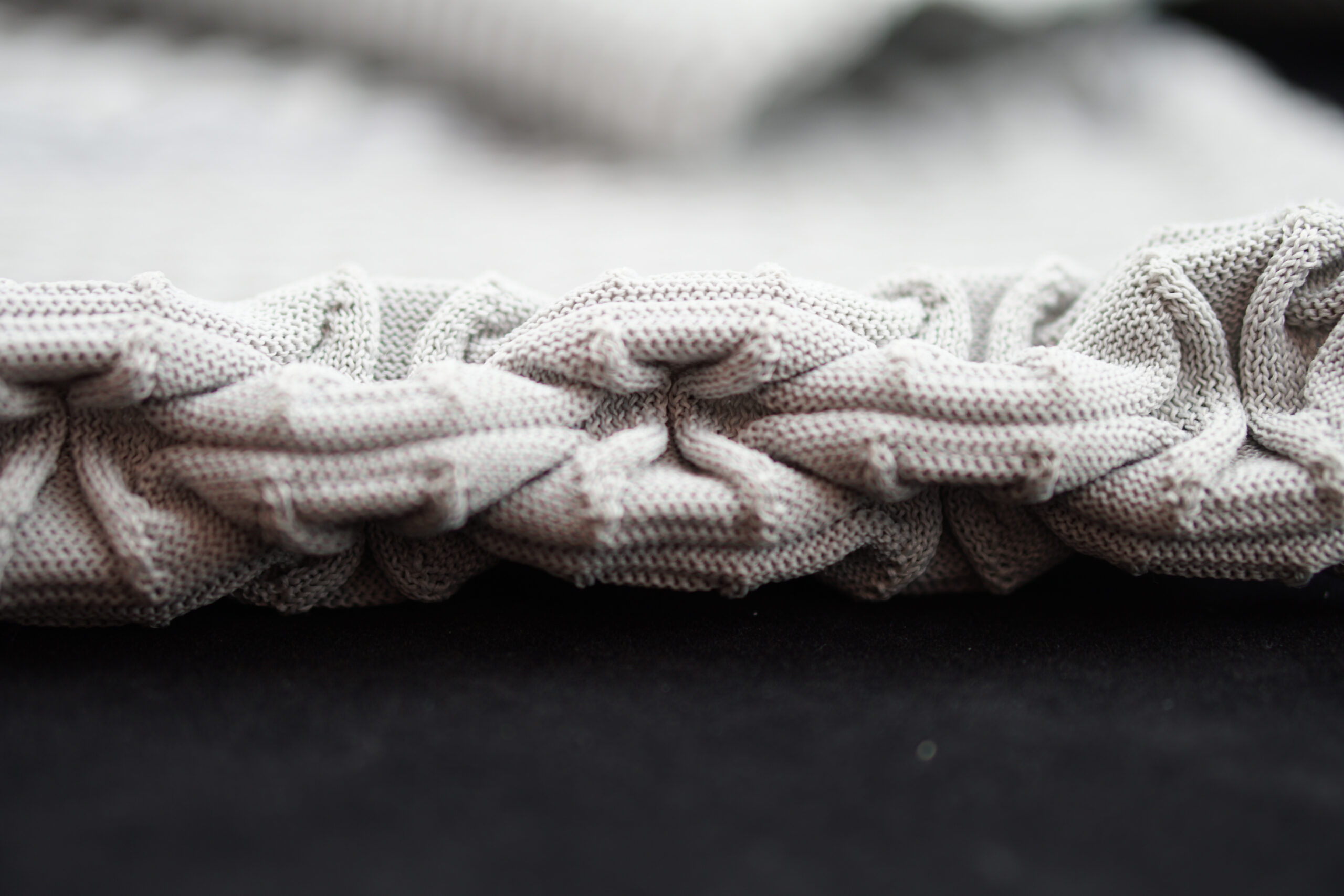
With its extensive background in textile technology, Drexel is well-equipped to take on prototyping challenges, owing to Dion’s initial decision to work with weft knitting machines in her lab.
Weft machines are known for being a bit more user-friendly than other textile manufacturing equipment, making them well suited for rapid prototyping and research and development. As a result, weft knitting has emerged as a promising technology for advanced textile research, and it is now a staple in leading functional fabric labs across Europe and Asia. Drexel’s center houses seven of them, along with a complement of other textile manufacturing equipment, including weaving and warp knitting machines.
It’s the closest textile-making analog to 3D printing, according to Stephanie Rodgers, director of Advanced Product Development at corporate partner Apex Mills, a specialty textile manufacturer in Graham, North Carolina. Just as a 3D printer extrudes its filament material to form a complete structure, a weft machine can knit a complete textile structure using a single strand of yarn. This means it is possible to fully control the architecture of a textile and to quickly produce small prototypes for testing.
“There is a real advantage to using weft knitting in developing technical textiles,” Rodgers says. “When you’re working with expensive, specialty yarns and you’re not entirely sure the prototype will work, or if the client will like it, you want to be able to iterate quickly on a small scale and without much material waste.”
Creating prototypes without a cut-and-sew step also benefits innovators looking to use electrically conductive yarns to add specific functions to textiles.
“The practical advantage of this is very big, because there is a strong necessity to minimize the number of conducting strands in your device, so that you can simplify the connection of the textile to a conventional electronic circuit,” says Alexey Melishchuk, associate director of licensing in Drexel’s Office of Research & Innovation, who is responsible for managing the intellectual property created at the center.
“People come up with all varieties of buttons and connecting clips and post-processing steps,” he says, “but it’s done in a bulky and clumsy way that’s inconvenient and not as robust. Having a single conductive strand passing through the entire garment allows you to have a complete electrical circuit and to do things like turning the garment into an antenna or connecting it to software that can determine where on the garment you touched it.”
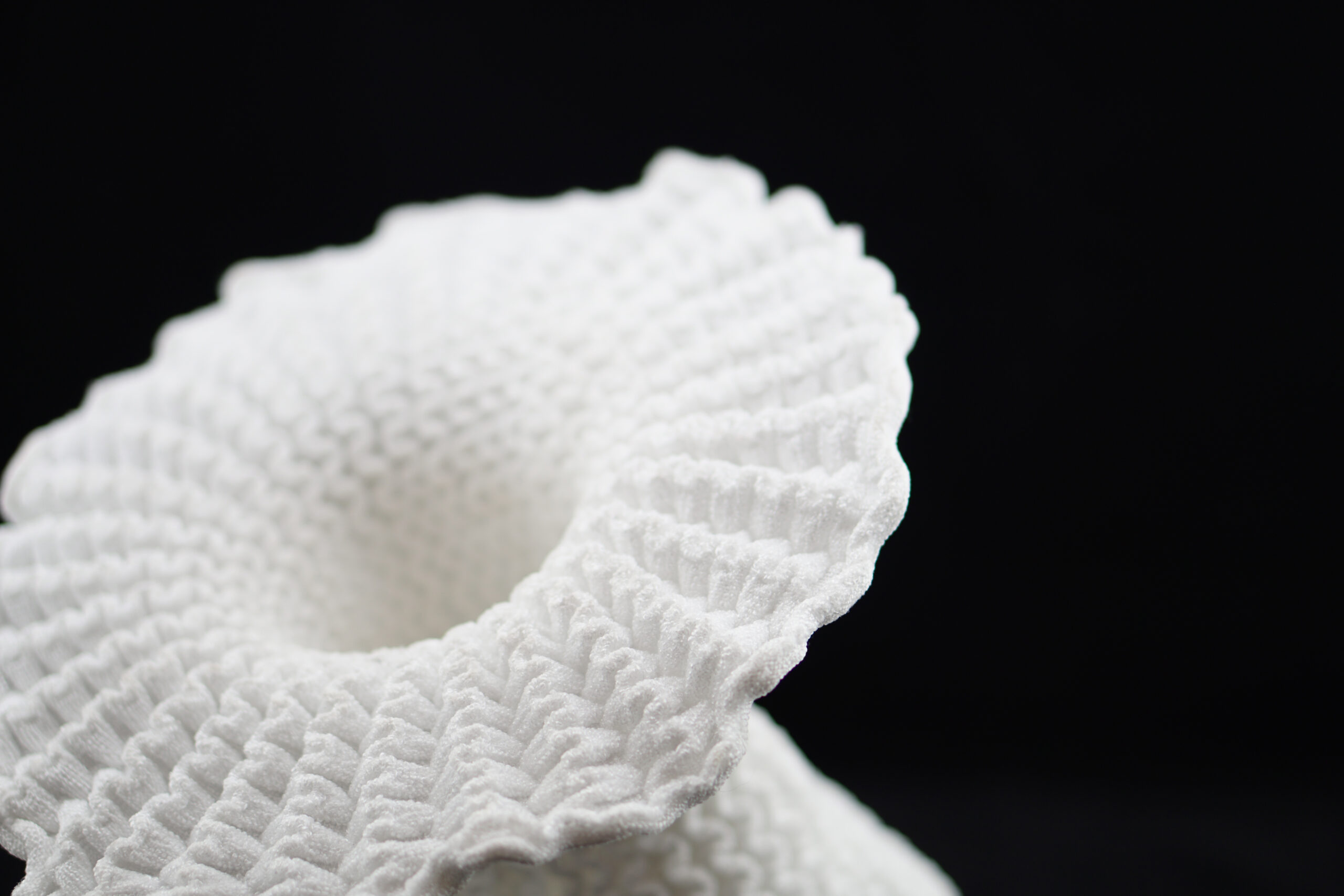
Drexel’s homegrown capacitive touch sensor (CTS) technology, which capitalizes on weft knitting for its functionality, is one of the team’s promising innovations. The fabric was initially developed by doctoral researcher Richard Vallett as a control system for humanoid robots. Through iteration and ongoing collaboration with Ali Shokoufandeh, a professor in Drexel’s College of Computing & Informatics, it has evolved into an internet of things–style touchpad kit. Textile engineers at the center have already used it to make a keyboard, a game controller and a track pad.
Dion saw the CTS as a technology that could help people understand the possibilities of functional fabrics. At Apex Mills, Rodgers, who was helping the company and its clients capitalize on fabric technology, also recognized the potential of the CTS as a proof-of-concept. She quickly connected with Drexel to translate it into a form factor that is warp-knit — another type of high-volume knit fabrication that is featured in Apex’s operation.
After Drexel’s initial weft-knit CTS patent, and a year of iteration and modification, Drexel and Apex Mills applied for a patent for the warp-knit technology and are integrating it into clothing, furniture and transportation as a remote-control system. Both the technology and the collaboration have been held up as a proof-of-concept throughout the AFFOA network.
The collaboration that produced the CTS exemplifies the transdisciplinary nature of the center’s work, according Dion. Projects typically involve a large team, with academic researchers at Drexel and elsewhere, and with industry partners, like Apex Mills.
“Before joining AFFOA, the Center for Functional Fabrics had a core competency in knitting and structures and integrating conductive fiber into a knitted structure — critical competencies to allow us to make smart textiles,” Luckowski says. “We didn’t explicitly have that capability at the headquarters, so we were looking to enhance our capability though regional strengths and also adding competencies we didn’t have somewhere else in the enterprise.”
Conductive fiber and yarn are key to expanding the capabilities of wearable technology, including devices that can monitor the health of the wearer, transmit information and communicate with other devices. But Dion emphasizes that the true test of any wearable technology is its ability to go unnoticed in everyday garments. For this to happen, the conductive fibers that comprise them must be sturdy enough to survive the knitting process, in addition to regular wear and tear.
Over the past several years, the team has been working with Drexel materials science researcher Yury Gogotsi to knit supercapacitors using yarn coated with a conductive material, called MXene, discovered in Drexel’s College of Engineering. Dion and her doctoral students explored various methods of modifying traditional processes to create MXene yarns that could not only provide the required electrical properties for smart textile applications, but also withstand the industrial knitting process.
The ultimate goal of all of these collaborations is to build a portfolio of next-generation innovations that can revive America’s domestic manufacturing economy and create new jobs. Manufacturing based on proprietary or highly technical textiles would restore resiliency to the country’s industrial production base and protect it against the type of supply chain chasms it experienced with personal protective equipment manufacturing during the pandemic, according to Luckowski.
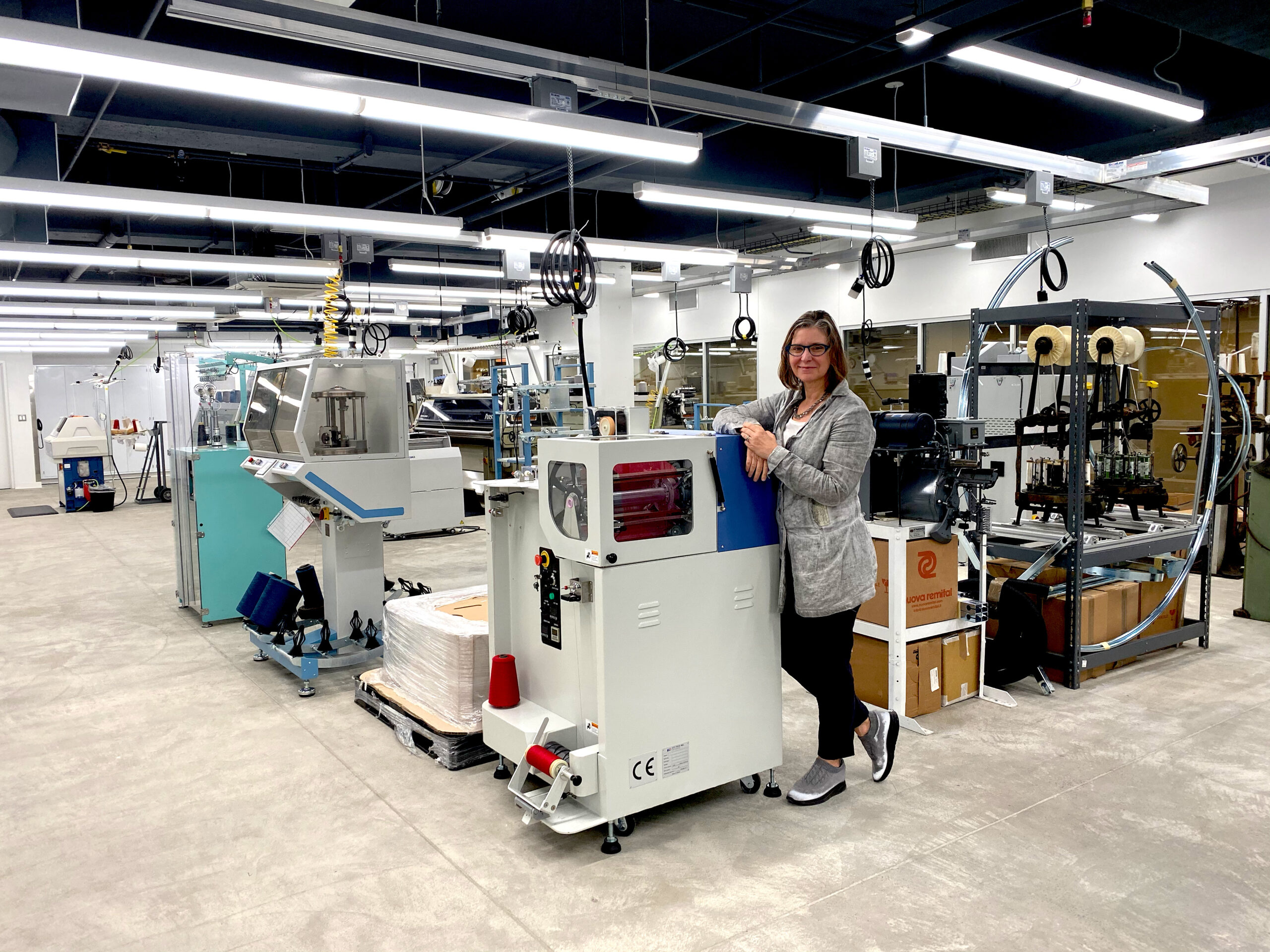
“The pandemic was definitely a wake-up call,” he recalls. “A silver lining is that people now recognize that if you can’t make it, you can’t have it. When you have a new model like this, you’re never done explaining it to people — some people need to see that tangible evidence, otherwise it’s just an abstraction.”
In the midst of the pandemic, the Center for Functional Fabrics proved its model can deliver.
Dion was able to reopen the center, initially shuttered by statewide lockdowns, as part of the relief effort. Within weeks, her team revamped its prototyping setup, turning it into a mask-making operation. Within the first three months, it had churned out 12,000 cloth masks for local frontline workers and community members. The center also created a filtration-testing operation with College of Engineering Professor Michael Waring for ongoing development of respirator masks and personal protective equipment, as part of a larger AFFOA COVID-19 response effort.
“Advanced manufacturing is very important because it may give us the opportunity to be able to pivot during difficult times,” says Dion. “That’s one of the things I always wanted the center to be about.”
Since her days as a bespoke fashion designer, Dion has demonstrated the vision to bring abstract ideas into reality. In the Center for Functional Fabrics, she has produced a prototype that might be just the thing to help others see the way forward.